Modelling and control of nonlinear compressor unit in biohydrogen plant using multivariable model predictive control (MMPC)
DOI:
https://doi.org/10.59190/stc.v3i3.232Keywords:
Biohydrogen Plant, Compressor, Ethylene Dichloride, MATLAB/Simulink, MMPCAbstract
Biohydrogen plants consist of several units, one of them is the compressor unit. The compressor unit serves to increase the pressure needed for the next processing unit. In real conditions, several disturbances may occur in the process, affecting the stability of the system. Therefore, process control is needed for this system. Co-simulation is done by integrating Aspen plus dynamics for the nonlinear model of the compressor unit and MATLAB/Simulink for the control system model and mathematical calculation. Multivariable model predictive control (MMPC) is considered to control the system of the compressor unit. Three MPC parameters such as sampling time (Ts), prediction horizon (P), and control horizon (M) are set to 0.5, 50, and 30 seconds. The co-simulation gives various results. The highest overshoot is 19.6278 kPa in CV3 when SP on CV1 changed. The longest settling time occurred in CV4 when SP in CV4 was changed, 47.2729 seconds. The highest IAE is 14.8831, which occurred in CV4 when the SP of CV4 changed, and ISE is 200.7517 in CV3 when the SP of CV1 is altered.
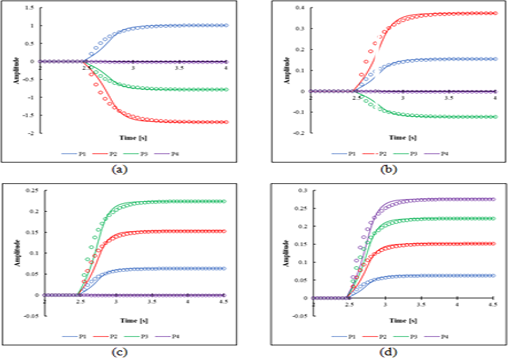
Downloads
Published
How to Cite
Issue
Section
License
Copyright (c) 2023 Science, Technology and Communication Journal

This work is licensed under a Creative Commons Attribution 4.0 International License.